HOW WE WORK
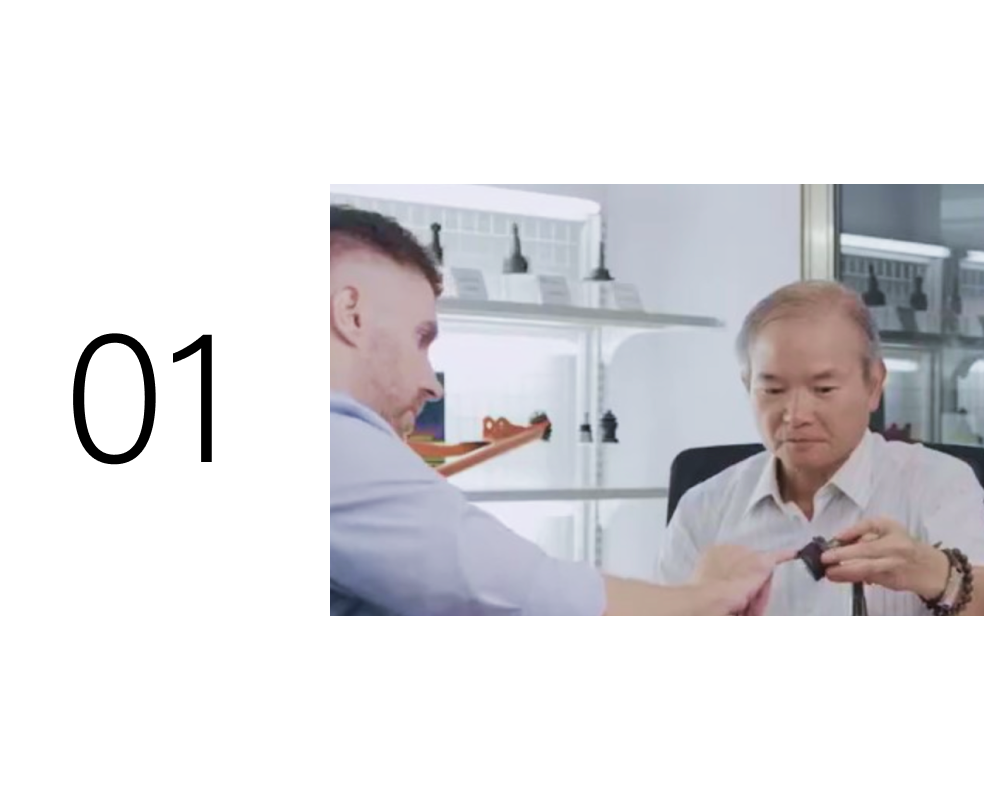
Contact Motorpro
Brand often provide concept or a defective OR sample for engineering analysis to prepare solution package suitable for brand EAU.
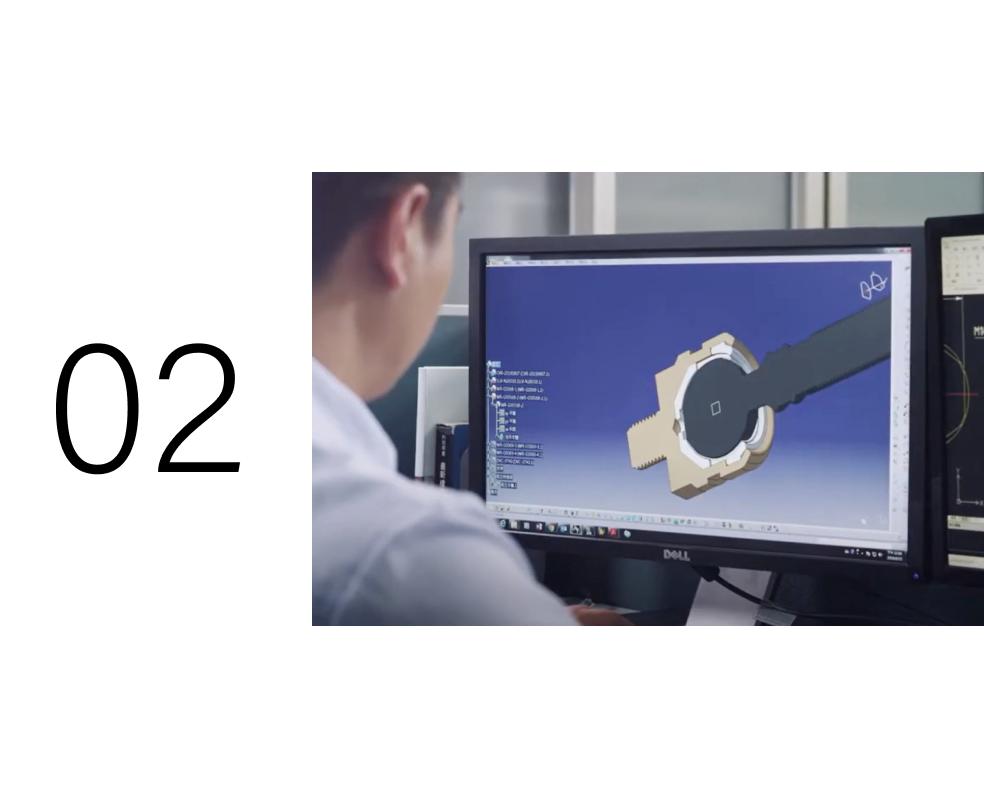
Review Drawing and Confirm with Motorpro
Evaluate detailed drawing and refine concept with Motorpro through co-creation.
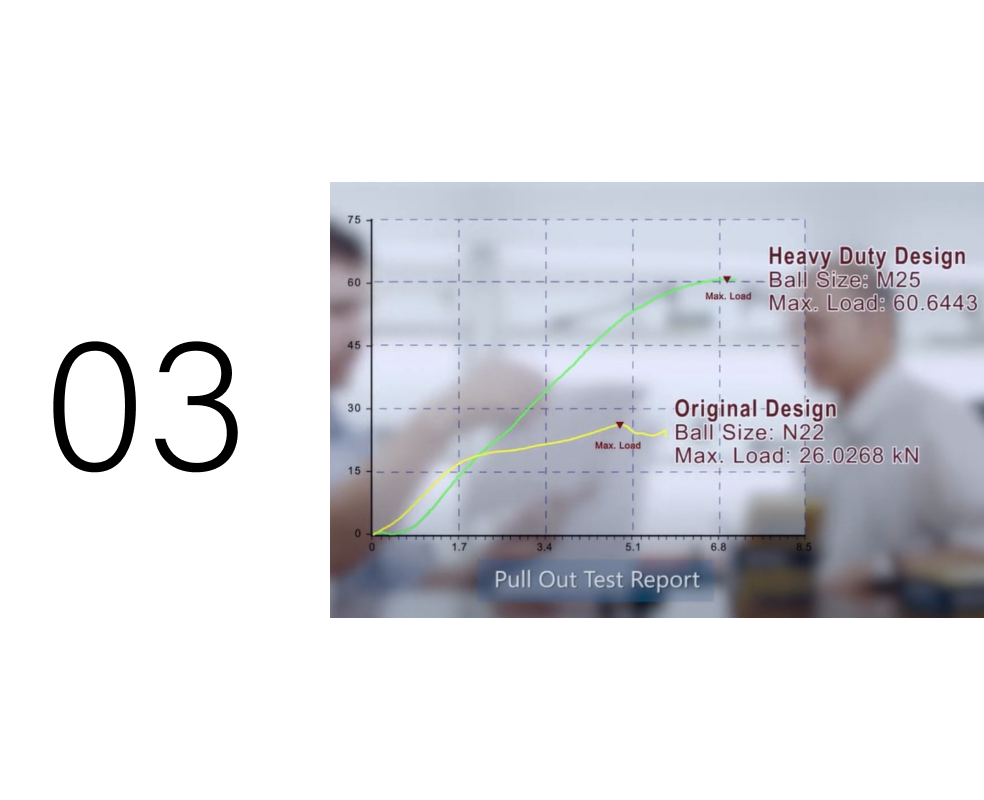
Data-Driven Design Refinement
Prototypes are developed and under extensive in-house testing includes hardness, pull-out and much more by Motorpro to ensure optimal performance.
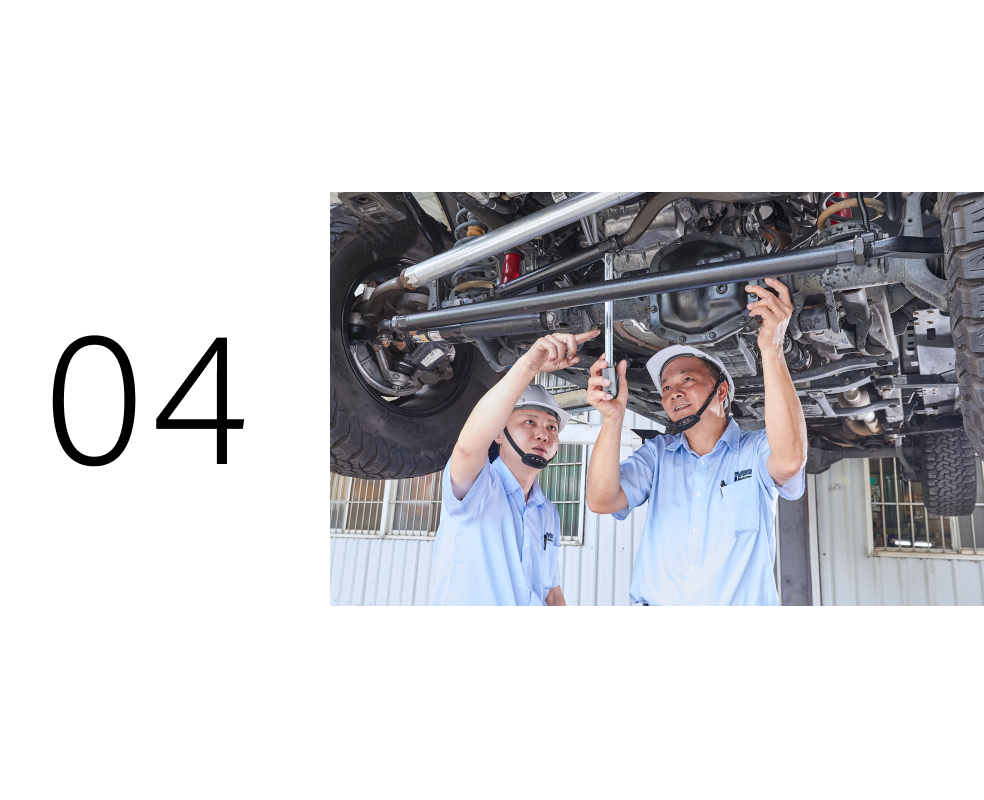
Pre-Production and Field Testing
Pre-production samples are created in our advanced production facility and will be shipped to you for on-vehicle field test trial to demonstrate the enhanced reliability of the design.
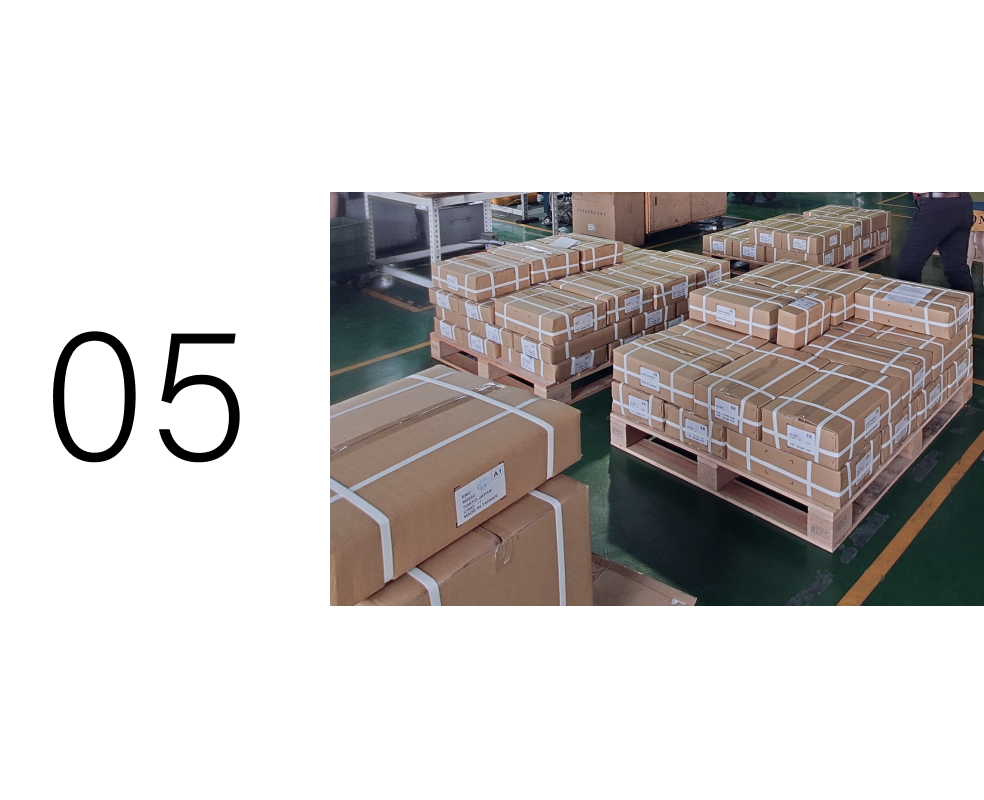
Mass Production and Delivery
Production and Quality Assurance: Products are manufactured in MotorPro’s TÜV NORD ISO9001:2015 certified facility in Taiwan, known for its 30 years of exceptional craftsmanship. Each shipment is accompanied by comprehensive lab test results for quality assurance and reference.
QUALITY ASSURANCE
IN-HOUSE TESTING CAPABILITIES
FAQ
How could you improve on my current or target design?
With nearly 30 years of experience serving major auto brands like Jeep, Toyota, Ford, and Dodge, we have a solid foundation in improving extreme duty designs. Most customers come to us with a specific model and part in mind for improvement, while others have unique designs that need feasibility and producibility checks. We start by understanding your goals, both engineering and financial, and then work backwards, tackling challenges step by step and validating them with our in-house test lab. Contact us to start a conversation.
How is your product different from others?
We are an engineering solution provider with a production facility in Taiwan, focusing on extreme duty components. This means your parts are designed and manufactured in Taiwan, undergoing rigorous in-house testing to meet our stringent internal standards, which surpass many international standards. Additionally, we closely manage all our suppliers in Taiwan to ensure consistent quality, reducing the likelihood of inconsistencies.
How is your service different from others?
We begin with concept development, proceed to mock-ups, and fully test these in our in-house lab. This means we are not just a manufacturer but also your QC partner, utilizing our advanced equipment. Learn more about the MotorPro Lab in the About Us section. We have been the driving force behind several well-known automobile brands, understanding the importance of honesty, dependability, confidentiality, and collaboration in building a brand you can trust.
What service does MotorPro provide? How is MotorPro different from other autopart manufacturers?
We assist from ideation to production. This includes CAD design, BOM creation, cost analysis, lab testing and reports, production of one-off samples, pilot runs, mass production, and after-sales service.
How could we start collaborating?
Reach out easily by visiting the "Contact Us" page. Share a few words about your needs so we can focus and get back to you promptly.
How can MotorPro assist me in growing my brand and reaching financial goals?
Once you contact us, we become your chief design architect, offering solutions that solve engineering problems. With extensive experience, we have developed multiple modular solutions that perform well and are cost-effective to meet market demands. Contact us with your questions, and we'll take it from there.
What do you do during a collaboration when "problems" arise?
Even with world-class operations, issues can occasionally arise. If this happens, we ensure the problem definition aligns with our client's perspective, identifying when, where, and how it occurred. We guarantee a response within 3 days. When necessary, you are backed by our insurance plan.